1
Green Issues
In Design
 |
Fez, Morocco. Ancient dye baths and traditions still being carried out today |
Ecology Evolution : Foreword
A brief review of Design Journal.
I have always been interested in the re-emerging systems of local manufacturers and locally sourced materials, sourcing natural plant dyes from the landscape intrigued me. I set out to research the subject of natural dying, knowing through my knitwear career the historical values of earthy colours and the natural colours syrupy plant dyes can create.
Wishing to avoid synthetic chemicals dyes and having knowledge through my grandfathers occupation as an industrial chemist dyeing fabrics for Coutaulds. While growing up he taught me how to dye from nature as a child by adding this process into my childhood play(dyeing mini hanker-chiefs for the fairies and small animals in his garden for me).My grandfather was eventually awarded for his sustainable dye practices by the WWF (world wide life foundation).
Making inks from natural materials was the main process for removing synthetic materials from my printing project and proved to be the most sustainable way to design compared to the other processes I tested within the five test projects trails within my brief.
I set out to initially create my own dyes, then I developed my own inks for screen printing. One book that I used for most of my knowledge was botanical inks by Babs Behan, more details of my practical processes can be found on my blog ’naturesarmour.blogspot.com’
Developing my printed ink for screen printing was developed from an online makers video clip, this and my testing organic printed ink for printing can be viewed via (Appendix.V)
Drawing ink using plant pigment.
After using a dye bath for dying fabric swatches I boiled down the remaining residue in order to make a drawing ink.
I used 2 tsp of plant pigment, 2 tsp of gum Arabic , 1 tsp of vinegar and 1 tsp of salt.
Return to heat and simmer to get a thicker consistency.
 |
writing ink developed through natural plant pigments. |
My first attempt at drawing ink, it worked better with a paint brush was a bit drippy using a ink pen (traditional calligraphy pen).
Natural dyes using Hunting and Gathering technique.
Potentially dying fabrics using natural resources is a eco conscious sustainable process that has been done for centuries and centuries. Removing chemical compound dyes from the system is a good way to help the natural earth combat environmental damage.
I have started the process of creating my own dyes and solutions to create natural colours from the environment and what would potentially be wasted, can be used to create great colours.
 |
Rhubarb leaf for mordants and dyes. |
Rhubarb leafs make great mordants for animal fibres and can also be used as a colour modifier.
 |
Chopped Rhubarb leaf for boiling. |
Chopped Rhubarb leafs before cooking in water for 1 hour.
 |
Rhubarb solution for mordant and dye. |
Mordant solution created.
 |
Avocado dye bath |
Avocado pip dye bath boiled for 1 hour before adding fabric.
 |
Avocado fabric swatch dye. |
Fabric swatches dyes using avocado pip.
Iron Water is useful to use as a Mordant it fix’s vegetable fibre and can also brighten colour tones when dyeing fabric.
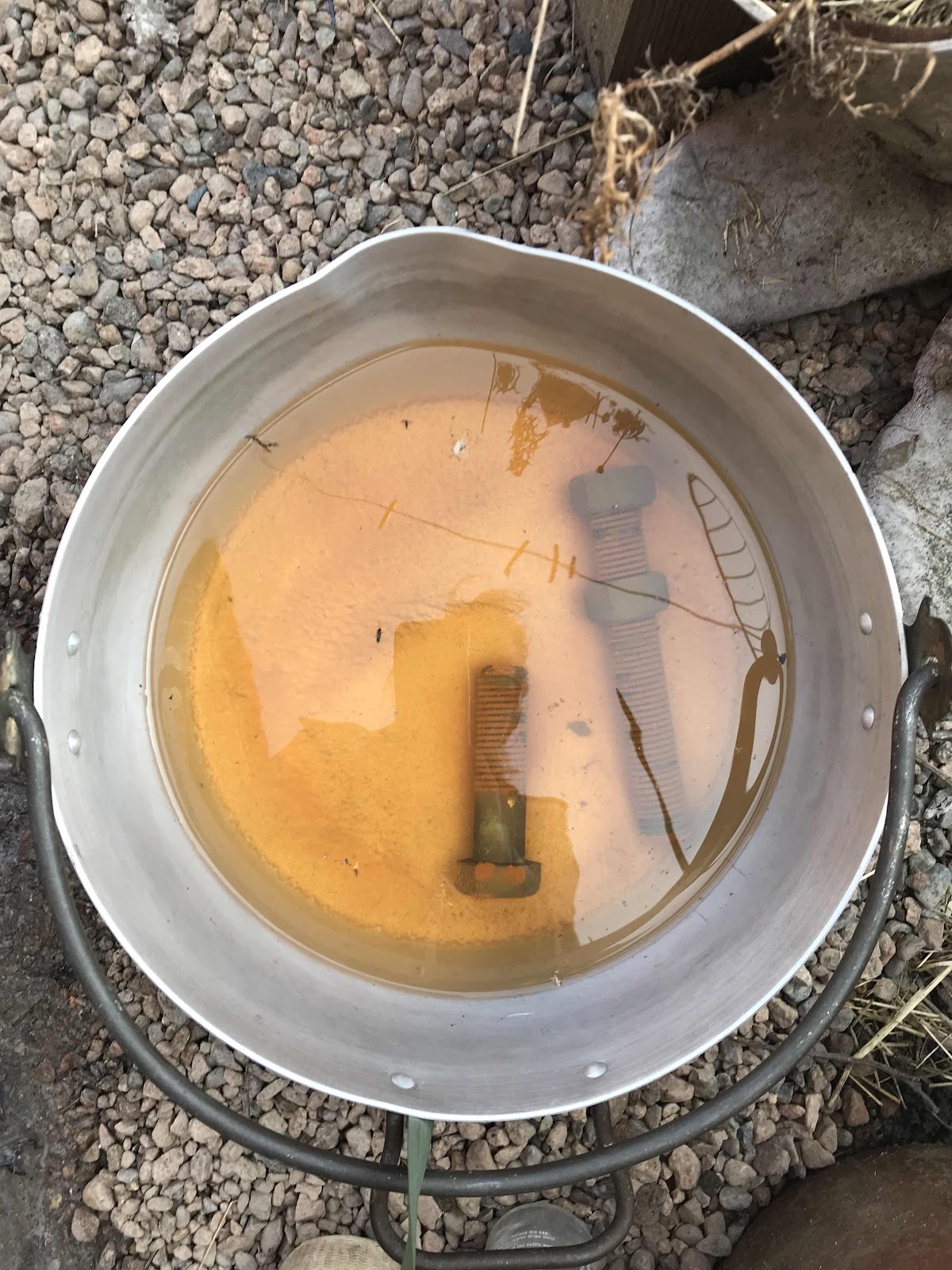 |
Mordant Iron water. |
Old nuts and blots can create a great mordant for fabric dying.
Wild Nettle
Hunting and gathering from your local surroundings is a great way to dye your own fabrics. Try not to pull up the roots, using scissors and gloves cut 3/4 leafs down from the top.
You need 200% more than the dry weight of your fabric. I have cut 100 grams of nettle add boiling water to nettles and add up with warm water. Leave in water for 1-2 days use a suitable mordant for your fabric.
 |
Wild nettle chopped for boiling. |
Chopped Nettle.Sock in water for 1-2 days to soak out the natural dye.
After 2 days in water, drain plant material to reveal deep green almost black dye solution.
 |
Nettle dye solution. |
Use a Rhubarb mordant for animal fibre .
ie silk or wool.
 |
Silk soaking in Rhubarb mordant before dying. |
Cotton woven squares soaking in Rhubarb mordant, soak for a few hours of over night. Wash in Ph balanced un perfumed soap.
Blackberry dye
Using a small bag of blackberries boil in water for 1 hour, drain into a jar throw away pulp(mash berries when cooking). Add pre wetted, pre mordent fabric. Boil for 1 hour for strongest colour less for lighter colour. Use one part fabric to one part dye amount, making sure you cover fabric.
 |
blackberry dye bath. |
Hot dye bath simmer for one hour Blackberry.
 |
Blackberry dye swatches/Cotton. |
Dye samples in Cotton using Oakgall mordant and blackberry dye bath.
 |
Blackberry dyed swatches on silk. Rhubarb dye silk sample on right. |
Silk samples dyed in blackberry dye and one dyed in Rhubarb which is also used as a mordant.
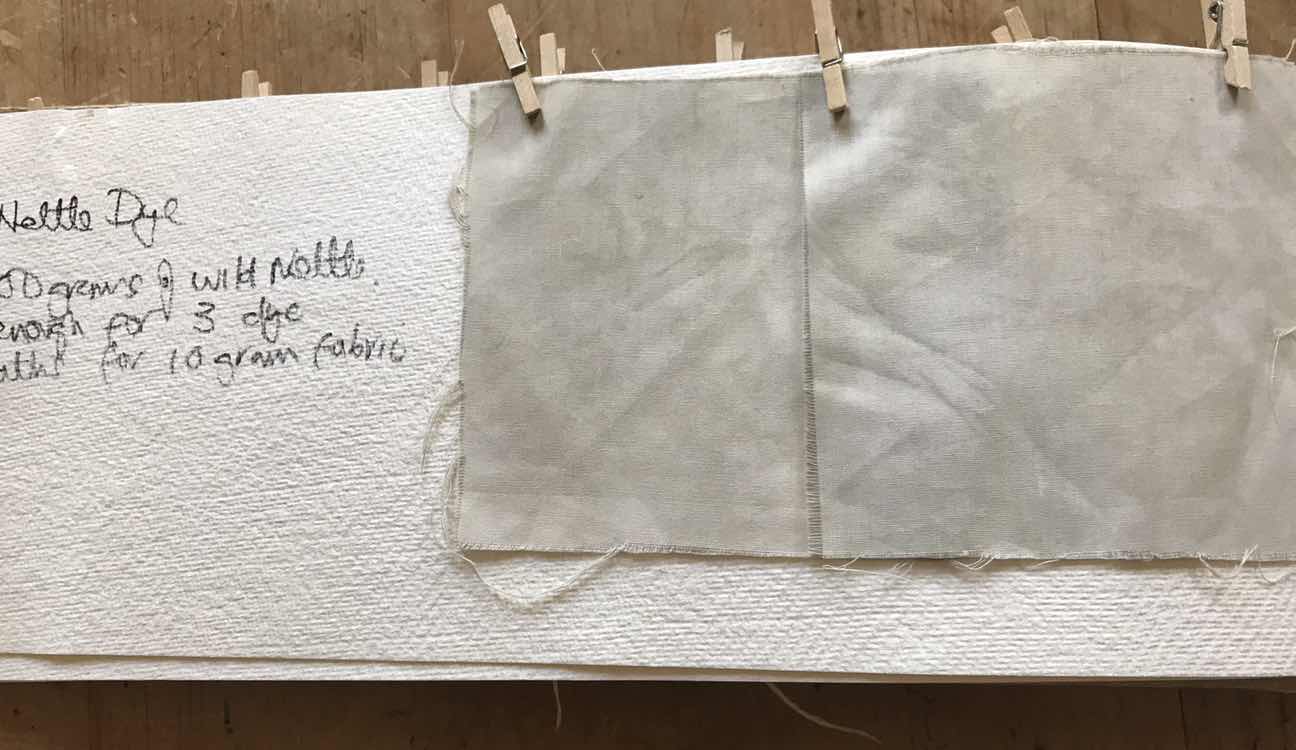 |
Nettle dye samples on Cotton. |
Nettle dye.
 |
Nettle dye on silk. |
Nettle dye onto silk with Rhubarb mordant added before dye bath.
 |
Up cycled coffee bean dyed fabrics. |
Left over used coffee granules from natural coffee bean. Pre mordant oak gall on the cotton swatches on the right. Silk swatch on the left using pre mordant rhubarb leaf.
 |
Indigo dye fabric swatches. |
Woad dye bath used in ancient celt and saxon culture to dye fabrics and paint warriors faces before battles. It comes from a locally found natural forna.
Indigo dye.
Indigo vat dye is different to most dye vats as it is not soluble in water, it needs some chemistry to allow the pigment to attach to the fabric. The oxygen in the water needs to be removed using slaked lime (Calcium Hydroxide. Using gloves, goggles and mask is needed for safety reasons.)
 |
Equipment and materials. |
Equipment and ingredients needed for indigo dyeing.
Indigo dye vats take a long time to prepare. Indigo does not naturally dissolve in water. A chemical reaction is required to remove the oxygen which allows the indigo to fix to fabrics. In ancient times this was done through fermentation which took weeks to work. Indigo also does not work well when heated directly so a bam baree must be used.
 |
preparations for dying indigo. |
Bam baree should be used when heating indigo.
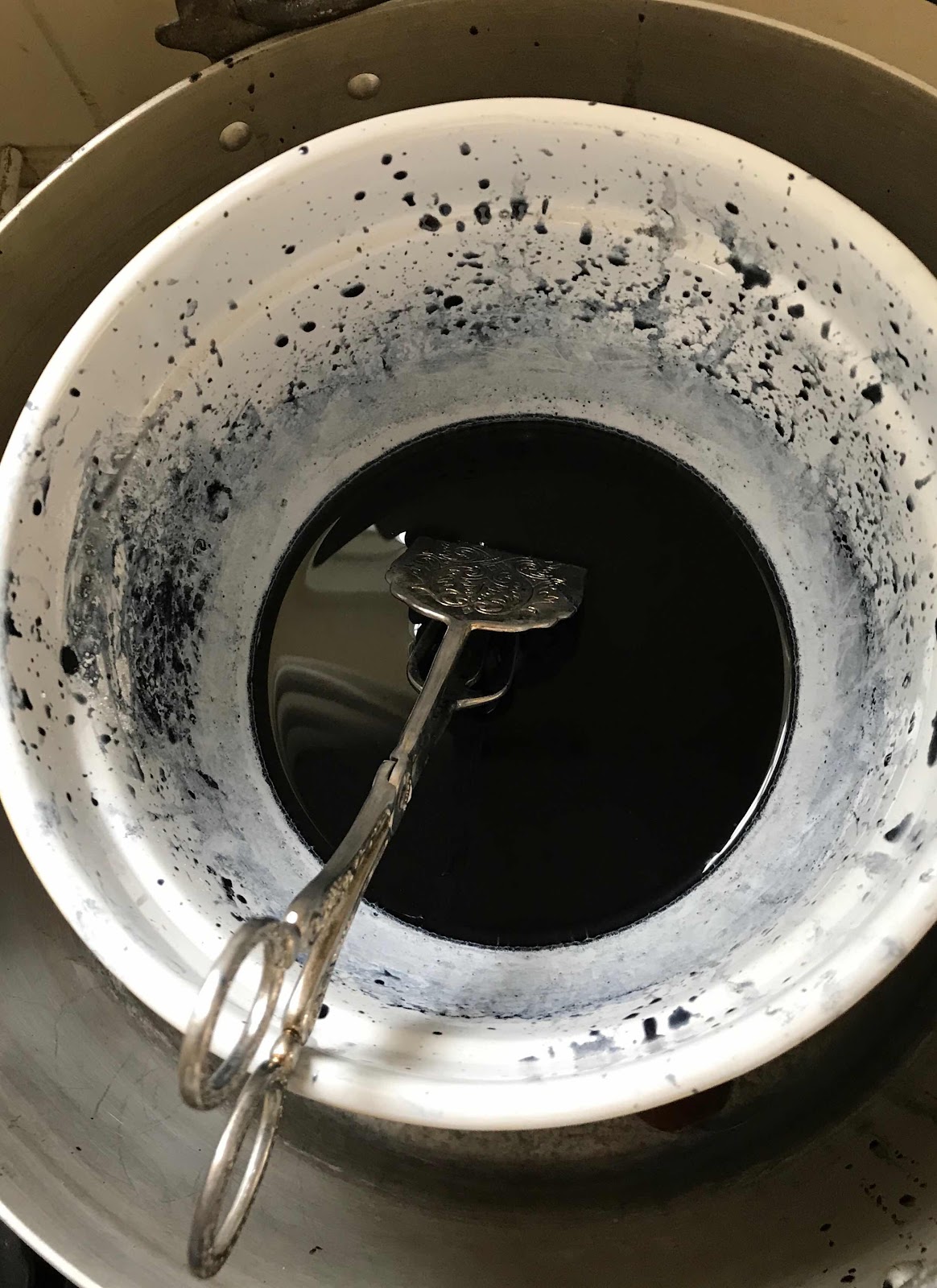 |
Indigo dye bath. |
I used my own version of fructose syrup as I found it difficult to purchase.The vat should go a green colour when the oxygen leaves the liquid which helps with the pigment fixing to the fabric. I think I could do with buying some fructose and doing another vat test the results.(Another name for fructose is fruit sugar)
 |
Indigo dye swatch results. |
One dip in vat results.
 |
Indigo dye on raw silk and cotton. |
3 dips in vat using silk on the left and cotton on the right. There is some blotching visible which could have something to do with my version of fructose. The vat should have gone a green colour and it didn’t. The answer is to do another dye bath using proper fruit sugar.